Welcome to the future – Loop production turns automatic – We make you leader of your business – Master of the saw loop production
A MASTER OF LOOPS
We are excited to announce the next phase of our ground-breaking Loopmaster. Loopmaster not only streamlines operations but also empowers human workers by improving safety, quality, and overall job satisfaction. It’s a win-win for both technology and people!
With advanced features that optimise operations and improve production quality, the Loopmaster will transform the future of work.
We have already delivered three units to key locations, and these customers can now experience the power of this state-of-the-art technology first-hand. And over the coming months, we will be delivering two more units.
Watch the video and follow us on this innovative journey!
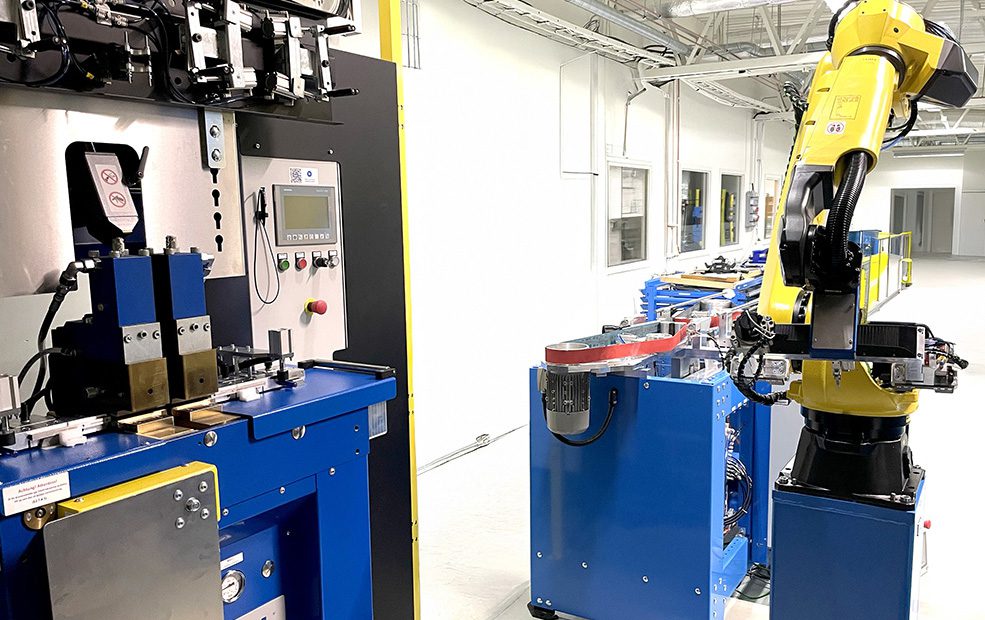
EXPERIENCE THE FUTURE OF GRINDING
Loopmaster’s latest innovation – the fully automated Grindcommander, designed to boost production efficiency and enhance weld quality like never before.
Setting a new industry standard, the Grindcommander combines cutting-edge automation and full process control to deliver superior, repeatable results with every cycle.
To find out more, contact our sales team today!
MEET THE LOOPMASTER
Designed to be a flexible system, Loopmaster seamlessly adapts to your production needs. Whether you are producing high-capacity bi-metal blades or other blade types, Loopmaster delivers exceptional results. Say goodbye to tedious changeovers – our system easily produces welded loops of varying lengths from the same master coil, streamlining your entire manufacturing process.
The system comprises:
- ALO 177 Cut to length machine with match finder system
- FANUC M20iD35 6 axis industrial robot
- Band gripping/manipulating robot tool
- Loopmaster table
- Operator panel/HMI
- Protective fence
- ALO 106 Cube
- ALO 106-E Cube elevator
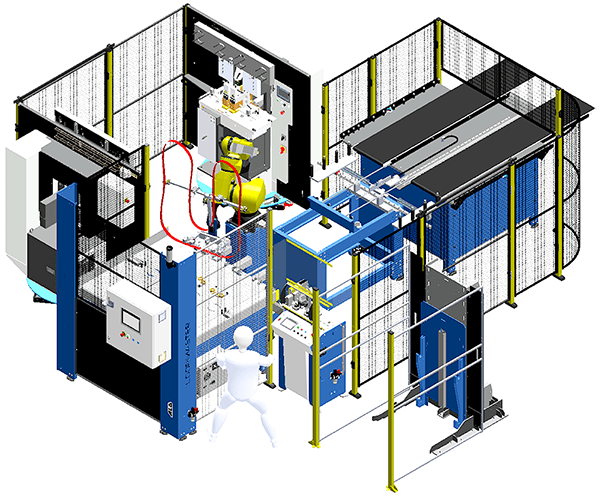
FLEXIBLE AND SCALEABLE
The Loopmaster can serve up to three weld units, realizing an output of up to 80* loops per hour, Each loop can have a length between 2.0 – 6.8 meters and you can order up to three different length in one batch – effectivly minimizing set times and maximates your production
Need to manually weld a loop, or service a weld unit? With the optional turn table, each unit can be turned out of the cell for manual operation or service, while the Loopmaster continues the production on the other available units.
* With three weld units and a cycle time of 45 seconds.
MODULAR DESIGN
The system is based on our popular ALO 177 Cut-to-length machine, and if you already have one then you have already started your journey into the Loopmaster concept!
With up to three weld units, the flexibility of the system will be at its maximum capacity. Each unit can be set up dedicated to different
blade dimensions, or all units for one blade dimension – what ever suits your production best!
Add the loop table, robot and minimum one welder, and you’re good to go! Contact us today for a quotation!
177 – THE HEART OF THE LOOPMASTER
The ALO CTL machine revolutionised the cut-to-length process of band saws by introducing advanced automation and precision. It is excellent for handling both large volume orders and single-piece orders with ease. Capable of utilising smart barcode and QR-code technology, the machine can be set up quickly and efficiently. It is the first of its kind to replicate the complicated manual tooth matching process, ensuring high accuracy.
The innovative Matchfinder system significantly reduces scrap pieces, enhancing material efficiency. The CTL machine’s user-friendly interface and sophisticated capabilities make it a game-changer in the industry.
177 is the foundation of the Loopmaster concept. Old versions of 177 are fully compatible with the Loopmaster concept but to unlock new levels of productivity – upgrade your 177 to the latest mark version.
WHAT’S NEXT IN THE LOOPMASTER CONCEPT?
We’re excited to introduce the next steps in the project. This year, we’re launching the automatic grinding machine.
Later this year, look forward to the third step in the Loopmaster project: the automatic capping machine. This updated version of the 123 will bring further advancements and efficiency to your operations.
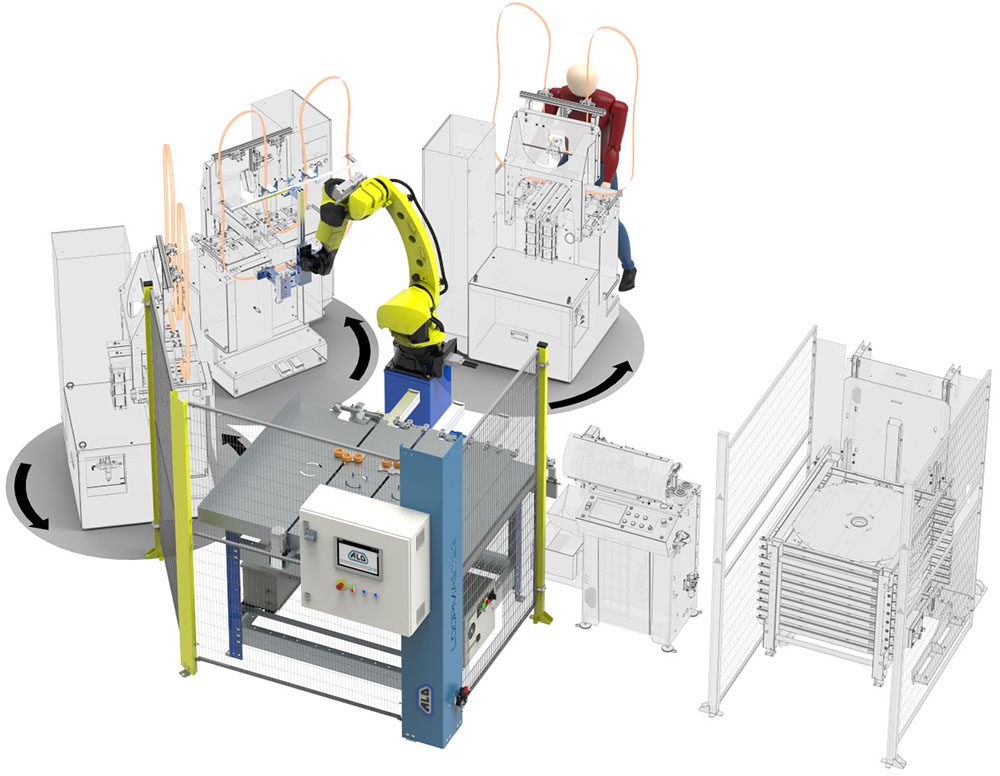